Casting Study: Foot Pedal Level
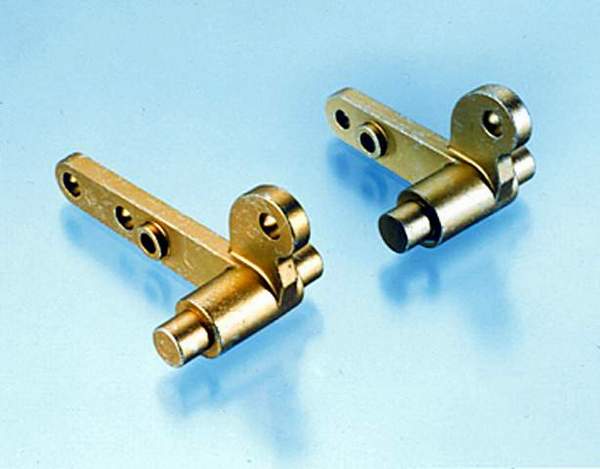
The lever was originally designed as a steel sand casting with machining operations to size the shaft, pivot hubs, and cable connection holes. The final operation was a zinc plating. After a value analysis of an all-metal foot pedal control system, the materials management team determined that the lever, which connects the modulator and throttle cables to the pedal assembly, could produce sizeable cost savings. The lever is now redesigned as a Zamak 3 die casting, with all the strength required for the application. The first thing the redesign accomplished was the combination of two different-sized levers. One lever was needed for two-inch cable travel and another for three-inch travel. The single die-cast lever combines the two and provides connecting holes for either travel length. In addition to eliminating a part number and reducing inventory, zinc die casting also eliminated all secondary machining. The process holds the required hole diameter tolerance of +/-0.001 in. and the hub diameter tolerance of +0.002/-0.001 in. By redesigning the lever as a zinc die casting, the component cost was slashed 91 percent. This cost reduction provided a tooling payback period of 8.5 months.